


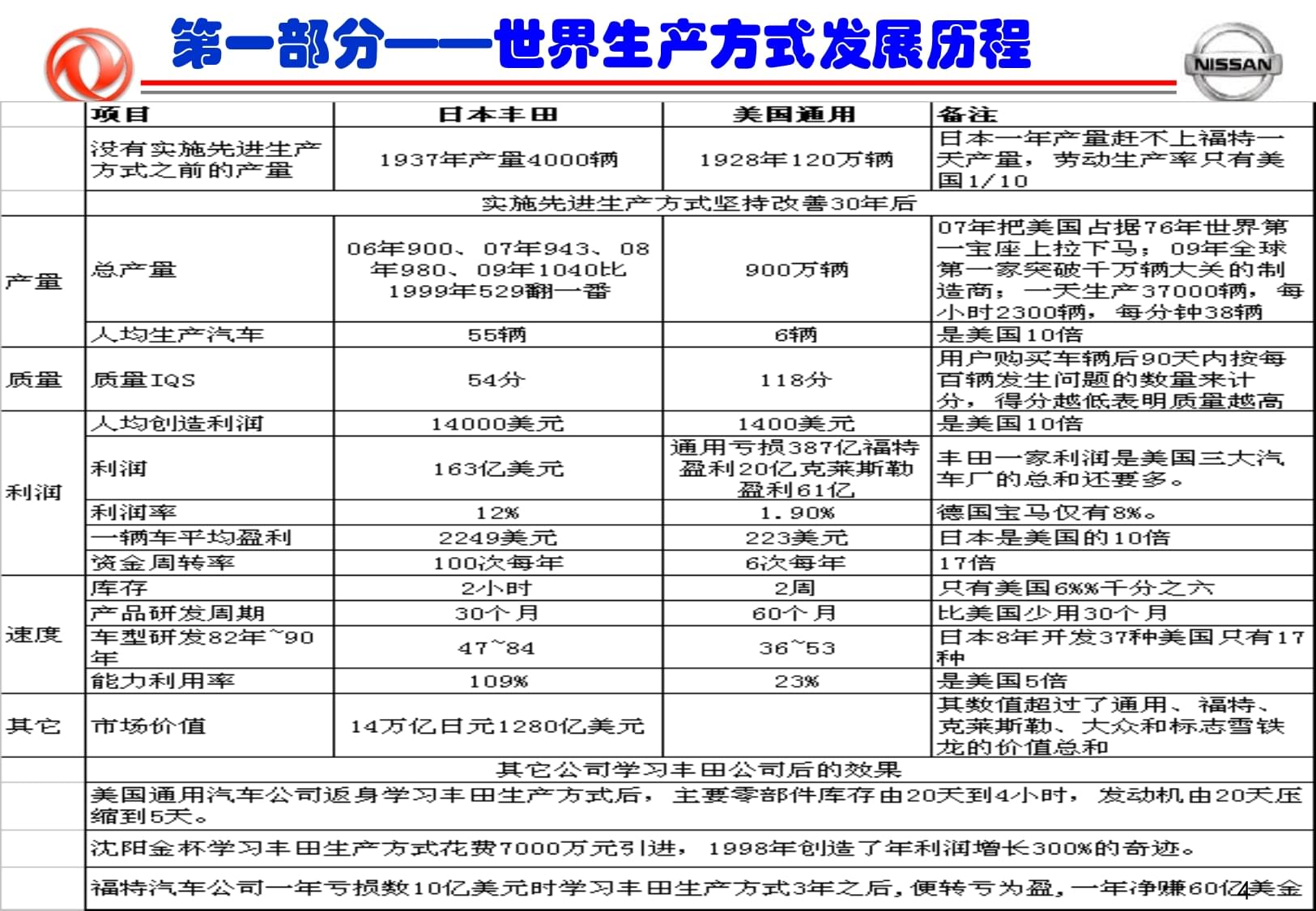

版權(quán)說明:本文檔由用戶提供并上傳,收益歸屬內(nèi)容提供方,若內(nèi)容存在侵權(quán),請進行舉報或認領(lǐng)
文檔簡介
內(nèi)容提要一、世界生產(chǎn)方式演變歷程
……………….……………..…二、精益生產(chǎn)概論……………….……………1、含義2、豐田生產(chǎn)基本構(gòu)架3、特點..三、精益生產(chǎn)推進……………….…………….四、如何降低成本減少浪費?……………….………….五、東風(fēng)公司精益生產(chǎn)實踐……………….…………….1第一部分——世界生產(chǎn)方式發(fā)展歷程2第一部分——世界生產(chǎn)方式發(fā)展歷程3第一部分——世界生產(chǎn)方式發(fā)展歷程4汽車業(yè)制造系統(tǒng)兩次大變革HenryFordAssemblylinemassproductionProduceinhighvolumewithlowvarietySingleskill福特首創(chuàng)的裝配線是大規(guī)模低品種生產(chǎn)方式的代表,工人被當(dāng)成工作的機器ToyotaProductionSystem(TPS)
豐田系統(tǒng)是建立在準時化觀念上的拉動式生產(chǎn)模式,以應(yīng)付小訂單多起源于20世紀50年代豐田汽車公司,而在80年代中期被歐美企業(yè)紛紛采用。隨著微利時代的來臨,精益生產(chǎn)模式成為企業(yè)競爭的有力武器品種的挑戰(zhàn)第一部分——世界生產(chǎn)方式發(fā)展歷程5(一)何謂精益生產(chǎn)方式Lean
Production精益生產(chǎn)
精益生產(chǎn)(LeanProduction)就是及時制造,消滅故障,消除一切浪費,向零缺陷、零庫存進軍。1960年代開始,以豐田為代表的日本汽車制造業(yè)通過實施JIT生產(chǎn)模式,以低成本、高質(zhì)量的突出優(yōu)勢迅速占領(lǐng)美國汽車市場,引發(fā)了美日之間長達十年的汽車貿(mào)易戰(zhàn)。它是美國麻省理工學(xué)院在做了大量的調(diào)查和對比后,認為日本豐田汽車公司的生產(chǎn)方式是最適用于現(xiàn)代制造企業(yè)的一種生產(chǎn)組織管理方式,稱之為“精益生產(chǎn)”,綜合了大量生產(chǎn)與單件生產(chǎn)方式的優(yōu)點,力求在大量生產(chǎn)中實現(xiàn)多品種和高質(zhì)量產(chǎn)品的低成本生產(chǎn)。JIT——因其經(jīng)營效率極限化被美國學(xué)者贊譽為“精益生產(chǎn)”,并對人類的生產(chǎn)革命產(chǎn)生了長遠影響。
第二部分——精益生產(chǎn)基本概論6日本豐田生產(chǎn)方式的老師實際是美國人的IE大野耐一:“什么是豐田生產(chǎn)方式,就是豐田式工業(yè)工程。”美國人又將豐田生產(chǎn)方式(TPS)概括為精益生產(chǎn)(LP)。IE工業(yè)工程(美國)TPS豐田生產(chǎn)方式(日本)LP精益生產(chǎn)(國際)TPS/LP=IE+企業(yè)文化=LP+精益文化第二部分——精益生產(chǎn)基本概論7JIT的基本思想是:只在需要的時候、按需要的量、生產(chǎn)所需的產(chǎn)品,故又被稱為準時制生產(chǎn)、適時生產(chǎn)方式、看板生產(chǎn)方式。JIT的核心是:零庫存和快速應(yīng)對市場變化。精益生產(chǎn)不斷消除所有不增加產(chǎn)品價值的工作,所以,精益是一種減少浪費的經(jīng)營哲學(xué)。JustIn
Time適品·適量·適時第二部分——精益生產(chǎn)基本概論81、“精益”釋義:精——少而精,不投入多余生產(chǎn)要素,只在適當(dāng)時間生產(chǎn)必要的產(chǎn)品益——所有經(jīng)營活動有益有效,具有經(jīng)濟性2、目的:通過消除企業(yè)所有環(huán)節(jié)上的不增值活動,來達到降低成本、縮短生產(chǎn)周期和改善質(zhì)量的消除一切浪費追求精益求精和不斷改善去掉一切不增值的活動第二部分——精益生產(chǎn)基本概論9Heijunka平順化
Averageddailyvolume&mixSmoothproductionscheduleStandardWork標(biāo)準作業(yè)Kaizen改善CreativeIdeaSuggestionSystem建議系統(tǒng)5S3P生產(chǎn)準備流程TPMSMEDVisualControlsKanbanJustInTimeTaktTimeOne-pieceFlowDownstreamPull(拉動生產(chǎn))Jidoka品質(zhì)內(nèi)置(自働化)Built-inqualityPokayoke5WhyHarmonyofman&machine人機工程OperationalExcellenceBestCost,Quality,DeliveryEmpoweredemployeesCustomerfocusedcultureTPS第二部分——精益生產(chǎn)基本概論10(二)豐田生產(chǎn)方式構(gòu)架豐田生產(chǎn)系統(tǒng)由下列要素組成:一、兩大支柱及時制生產(chǎn)(JustInTime)品質(zhì)內(nèi)置(Jidoka,自働化)二、地基平順化(Heijunka)標(biāo)準作業(yè)(StandardWork)改善(Kaizen)三、工具屋1、5S2、目視管理3、看板(Kanban)4、一分種換模法(SMED,快速換產(chǎn))5、全員生產(chǎn)維護(TPM)6、生產(chǎn)準備流程(3P)7、建議系統(tǒng)(SuggestionSystem)第二部分——精益生產(chǎn)基本概論11TPS-豐田生產(chǎn)系統(tǒng)豐田生產(chǎn)系統(tǒng)房屋結(jié)構(gòu)由大野耐一和Eiji
Toyoda發(fā)展而成,用來向員工和供應(yīng)商解釋不斷演進的豐田系統(tǒng)。該生產(chǎn)系統(tǒng)(TPS)的目的是消除運營中所有的muri,mura,muda(過載、不均衡、浪費)。這是一種讓每位員工參與進來,通過采用PDCA(計劃、執(zhí)行、檢查、糾正)的方法解決問題,改善質(zhì)量、成本、交貨期、安全和員工士氣。采用房屋結(jié)構(gòu)解釋豐田生產(chǎn)系統(tǒng)的原因在于,房頂、柱子和地基代表一種類似該系統(tǒng)的穩(wěn)定結(jié)構(gòu)。今天,豐田生產(chǎn)系統(tǒng)還在不斷的發(fā)展。豐田人開始稱豐田生產(chǎn)系統(tǒng)為“員工思考的系統(tǒng)”
來代替原有名稱。豐田系統(tǒng)總是不斷的改進。
豐田生產(chǎn)系統(tǒng)(TPS)是精益企業(yè)的運營藍圖大多數(shù)成功實施精益的組織都采用豐田生產(chǎn)系統(tǒng)作為他們的運營藍圖。他們學(xué)習(xí)并理解該系統(tǒng),重新命名使其結(jié)合自身情況為其所用,同時盡可能采用純粹的豐田方式。
(二)豐田生產(chǎn)方式構(gòu)架第二部分——精益生產(chǎn)基本概論12豐田生產(chǎn)系統(tǒng)屋顯示了通過消除浪費持續(xù)改善達到世界級的生產(chǎn)系統(tǒng)。左邊支柱及時制生產(chǎn)(JIT)-節(jié)拍時間-流動-下游拉動)
消除生產(chǎn)中的7種浪費。使生產(chǎn)和信息平滑流動,最小化庫存和空間。右面支柱品質(zhì)內(nèi)置Jidoka(自働化)
在流程中內(nèi)建品質(zhì),使用智能自動化分離人工和機器作業(yè)。實施低成本的自動化、防錯法、設(shè)備更新和可靠性改進。
地基
平順化Heijunka
穩(wěn)定生產(chǎn)排程中的變動。降低整個交貨期時間,協(xié)調(diào)銷售、生產(chǎn)安排和顧客需求。第二部分——精益生產(chǎn)基本概論13(三)不同力量主導(dǎo)的生產(chǎn)方式比較項目生產(chǎn)企業(yè)主導(dǎo)消費者主導(dǎo)P(品種)少品種多生產(chǎn)一些好多品種量大固然好,品種也重要Q(質(zhì)量)防止投訴不良不可避免抽檢為中心高質(zhì)量構(gòu)建不產(chǎn)生不良的體系,全檢或零缺陷免檢C(成本)按成本定價成本+計劃利潤低價格將“干毛巾擰出水”,消除浪費D(交貨期)月單位交貨每月集中出貨快速交貨JITS(安全)生產(chǎn)優(yōu)先先保證出貨,安全嘛……安全第一符合標(biāo)準安全第一無工傷符合技術(shù)法規(guī)F(柔性)以產(chǎn)定銷只有這個能力……快速應(yīng)變隨時滿足第二部分——精益生產(chǎn)基本概論14項目手工生產(chǎn)方式大批量生產(chǎn)方式精益生產(chǎn)方式產(chǎn)品特點完全按顧客要求標(biāo)準化,品種單一品種多樣化、系列化設(shè)備和工裝通用、靈活、便宜專用、高效、昂貴柔性高、效率高作業(yè)分工與作業(yè)內(nèi)容粗略、豐富細致、簡單、重復(fù)較粗略、多技能、豐富對操作工人要求懂設(shè)計制造有較高操作技能不需要專業(yè)技能多技能庫存水平高高低制造成本高低更低產(chǎn)品質(zhì)量低高更高所適應(yīng)的市場時代極少量需求物資缺乏、供不應(yīng)求買方市場(三)不同生產(chǎn)方式的生產(chǎn)方式比較第二部分——精益生產(chǎn)基本概論15精益生產(chǎn)方式體系架構(gòu)意識改革*5S生產(chǎn)的快速與維護精益品質(zhì)保證與自動化柔性生產(chǎn)系統(tǒng)均衡化同步化現(xiàn)場IE作業(yè)研究生產(chǎn)設(shè)計與物流系統(tǒng)產(chǎn)品開發(fā)設(shè)計系統(tǒng)精益工廠追求7個“零”極限目標(biāo)Editedby(四)精益工廠追求7個“零”極限目標(biāo)第二部分——精益生產(chǎn)基本概論16(四)精益工廠追求7個“零”極限目標(biāo)“零”第二部分——精益生產(chǎn)基本概論177個“零”目標(biāo)零目標(biāo)目的現(xiàn)狀思考原則與方法零切換浪費多品種對應(yīng)切換時間長,切換后不穩(wěn)定·經(jīng)濟批量·物流方式JIT·生產(chǎn)計劃標(biāo)準化·作業(yè)管理·標(biāo)準化作業(yè)零庫存發(fā)現(xiàn)真正問題大量庫存造成成本高、周轉(zhuǎn)困難,且看不到真正的問題在哪里·探求必要庫存的原因·庫存規(guī)模的合理使用·均衡化生產(chǎn)·設(shè)備流水化零浪費降低成本“地下工廠”浪費嚴重,似乎無法發(fā)現(xiàn)、無法消除·整體能力協(xié)調(diào)·拉式生產(chǎn)徹底暴露問題·流程路線圖(四)精益工廠追求7個“零”極限目標(biāo)第二部分——精益生產(chǎn)基本概論187個“零”目標(biāo)零目標(biāo)目的現(xiàn)狀思考原則與方法零不良質(zhì)量保證低級錯誤頻發(fā),不良率高企,批量事故多發(fā),忙于“救火”·三不主義·零缺陷運動·工作質(zhì)量·全員質(zhì)量改善活動·自主研究活動·質(zhì)量改善工具運用零故障生產(chǎn)效率故障頻繁發(fā)生,加班加點與待工待料一樣多·效率管理·TPM全面設(shè)備維護·故障分析與故障源對策·初期清掃與自主維護零停滯縮短交貨期交貨期長、延遲交貨多顧客投訴多,加班加點、趕工趕料·同步化、均衡化·生產(chǎn)布局改善·設(shè)備小型化、專用化(四)精益工廠追求7個“零”極限目標(biāo)第二部分——精益生產(chǎn)基本概論197個“零”目標(biāo)零目標(biāo)目的現(xiàn)狀思考原則與方法零事故安全保證忙于趕貨疲于奔命,忽視安全事故頻發(fā),意識淡薄,人為事故多·安全第一·5S活動·KYT危險預(yù)知訓(xùn)練·定期巡查·安全教育活動·安全改善活動與傳統(tǒng)的大批量生產(chǎn)相比,精益生產(chǎn)只需要一半的人員、一半的生產(chǎn)場地、一半的投資、一半的生產(chǎn)周期、一半的產(chǎn)品開發(fā)時間和少得多的庫存,就能生產(chǎn)質(zhì)量更高、品種更多的產(chǎn)品。(四)精益工廠追求7個“零”極限目標(biāo)第二部分——精益生產(chǎn)基本概論20(五)精益生產(chǎn)-五個原則LeanManufacturing精益生產(chǎn)Value價值站在客戶的立場上ValueStream價值流從接單到發(fā)貨過程的一切活動Flow流動象開發(fā)的河流一樣通暢流動DemandPull需求拉動BTR-按需求生產(chǎn)Perfect完美沒有任何事物是完美的不斷改進降低成本,改善質(zhì)量,縮短生產(chǎn)周期第二部分——精益生產(chǎn)基本概論21(六)精益生產(chǎn)的重要特征一、建立看板體系。
就是重新改造流程,改變傳統(tǒng)由前端經(jīng)營者主導(dǎo)生產(chǎn)數(shù)量,重視后端顧客需求,后面的工程人員通過看板告訴前一項工程人員需求,比方零件需要多少,何時補貨,亦即是“逆向”去控制生產(chǎn)數(shù)量的供應(yīng)鏈模式,這種方式不僅能節(jié)省庫存成本(達到零庫存),更重要是將流程效率化。
二、強調(diào)實時存貨。
依據(jù)顧客需求,生產(chǎn)必要的東西,而在必要的時候,生產(chǎn)必要的量,這種豐田獨創(chuàng)的生產(chǎn)管理概念,在80年代即帶給美國企業(yè)變革的思維,現(xiàn)已經(jīng)有很多企業(yè)沿用并有成功的案例。
第二部分——精益生產(chǎn)基本概論22三、標(biāo)準作業(yè)徹底化。
他們對生產(chǎn)每個活動、內(nèi)容、順序、時間控制和結(jié)果等所有工作細節(jié)都制定了嚴格的規(guī)范,例如裝個輪胎、引擎需要幾分幾秒鐘。但這并不是說標(biāo)準是一成不變的,只要工作人員發(fā)現(xiàn)更好更有效率的方法,就可以變更標(biāo)準作業(yè),目的在于促進生產(chǎn)效率。四、排除浪費、不平及模糊等。
排除浪費任何一絲材料、人力、時間、能量、空間、程序、運搬或其他資源。即排除生產(chǎn)現(xiàn)場的各種不正常與不必要的工作或動作時間人力的浪費。這是豐田生產(chǎn)方式最基本的概念。排除浪費任何一絲材料、人力、時間、能量、空間、程序、運搬或其他資源。即排除生產(chǎn)現(xiàn)場的各種不正常與不必要的工作或動作時間人力的浪費。這是豐田生產(chǎn)方式最基本的概念。(六)精益生產(chǎn)的重要特征第二部分——精益生產(chǎn)基本概論23五、重復(fù)問五次為什么。
要求每個員工在每一項任何的作業(yè)環(huán)節(jié)里,都要重復(fù)的問為什么(Why),然后想如何做(How),以嚴謹?shù)膽B(tài)度打造完美的制造任務(wù)。六、生產(chǎn)平衡化。
豐田所謂平衡化指的是“取量均值性”。假如后工程生產(chǎn)作業(yè)取量變化大,則前作業(yè)工程必須準備最高量因而產(chǎn)生高庫存的浪費。所以豐田要求各生產(chǎn)工程取量盡可能達到平均值,也就是前后一致,為的是將需求與供應(yīng)達成平衡,降低庫存與生產(chǎn)浪費。七、充分運用“活人和活空間”。
在不斷的改善流程下,豐田發(fā)現(xiàn)生產(chǎn)量不變,生產(chǎn)空間卻可精簡許多,而這些剩余的空間,反而可以做靈活的運用;相同人員也是一樣,例如一個生產(chǎn)線原來六個人在組裝抽掉一個人,則那個人的工作空間自動縮小,空間空出來而工作由六個人變成五個人,原來那個人的工作被其他五人取代。這樣靈活的工作體系,豐田稱呼為“活人、活空間”即鼓勵員工都成為“多能工”以創(chuàng)造最高價值。
(六)精益生產(chǎn)的重要特征第二部分——精益生產(chǎn)基本概論24八、養(yǎng)成自動化習(xí)慣。
這里的自動化不僅是指機器系統(tǒng)的高品質(zhì),還包括人的自動化,也就是養(yǎng)成好的工作習(xí)慣,不斷學(xué)習(xí)創(chuàng)新,這是企業(yè)的責(zé)任。這點完全如松下幸之助所說:“做東西和做人一樣”,通過生產(chǎn)現(xiàn)場教育訓(xùn)練的不斷改進與激勵,成立學(xué)苑讓人員的素質(zhì)越來越高,反應(yīng)越快越精確九、彈性改變生產(chǎn)方式。
以前是生產(chǎn)線上(line)作業(yè)方式,一個步驟接著一個步驟組裝,但現(xiàn)在有時會視情況調(diào)整成幾個員工在一作業(yè)平臺(Cell)上同時作業(yè)生產(chǎn)。我曾參觀NEC的手機制造工廠,因為需同時生產(chǎn)二十幾種款式手機,所以激活機器人并無法發(fā)揮效率,他們就采用上述方式,一桌約三、四個員工作業(yè),來解決現(xiàn)場生產(chǎn)問題。(六)精益生產(chǎn)的重要特征第二部分——精益生產(chǎn)基本概論25JIT基礎(chǔ)認知易難足缺教育與訓(xùn)練自主研究會外部交流學(xué)習(xí)JIT規(guī)劃流線化生產(chǎn)外部顧問指導(dǎo)全員改善活動安定化生產(chǎn)管理的安定物量的安定質(zhì)量的安定設(shè)備的安定平衡化生產(chǎn)超市化生產(chǎn)及時生產(chǎn)消除浪費創(chuàng)造利潤人員的安定樣板線建設(shè)及推廣JIT生產(chǎn)技術(shù)運用(七)精益生產(chǎn)實施過程全貌第二部分——精益生產(chǎn)基本概論26精益生產(chǎn)方式推進順序1變換機種1.意識改革2.現(xiàn)場改善的基礎(chǔ)↓5S4.平準化5.標(biāo)準作業(yè)及時生產(chǎn)品質(zhì)保證自動化保全·安全少人化目視管理多工程操作3.流動生產(chǎn)看板Editedby第三部分——精益生產(chǎn)推進順序27精益生產(chǎn)方式推進順序2步驟1:意識改革步驟2:5S步驟2:流動生產(chǎn)步驟5:標(biāo)準作業(yè)JIT步驟4:平準化JIT舍棄陳舊的想法,采用JIT思想。JIT改善的基礎(chǔ)是整理、整頓、清掃、清潔、教養(yǎng)等5S停止大批制造,讓每一項工程都遵循順序來制造。不可有落單式制造,無論何時所生產(chǎn)的都是均等的數(shù)量。好不容易所完成的物品流程,不可弄亂,要牢記在心。第三部分——精益生產(chǎn)推進順序28為了對應(yīng)市場不斷變化的要求,力求以更少的人對應(yīng)生產(chǎn),以降低成本。①.明確劃分人與機械的工作,作業(yè)者盡可能讓機器獨立作業(yè),人與機械保持分離狀態(tài)。②.生產(chǎn)線作成U字形,機械設(shè)備改成自動化。③.將離島型的機器集中在一起,對于生產(chǎn)量而精簡人員,做到少人化。④.站立作業(yè)要徹底實施。⑤.作成工程聯(lián)系計劃表,培養(yǎng)技能多樣化?!嫔a(chǎn)方式推進順序3多工程操作Editedby第三部分——精益生產(chǎn)推進順序29為了對應(yīng)市場變化的要求,以更少的人對應(yīng)生產(chǎn),以降低成本。①.在設(shè)備或機械上,加裝輪子,是其可以簡易移動。②.不要有孤立的機械配置,集中在一處作業(yè),使生產(chǎn)線形成多工程操作。③.標(biāo)準化任何人都可以操作的簡單作業(yè)。④.訓(xùn)練員工成為掌握多種技能的能手。⑤.摒棄以工程定員的思想?!嫔a(chǎn)方式推進順序4少人化Editedby第三部分——精益生產(chǎn)推進順序30計劃安排好出產(chǎn)產(chǎn)品的品種、數(shù)量的時間及種類。①.將月產(chǎn)量、日產(chǎn)量換算成循環(huán)時間(循環(huán)鐘)。②.以“循環(huán)鐘”為基本,作成周期表。③.縮短變化準備及零件更換(機種切換)的時間。④.生產(chǎn)流程標(biāo)準化?!嫔a(chǎn)方式推進順序5平準化Editedby第三部分——精益生產(chǎn)推進順序31導(dǎo)入一種結(jié)構(gòu),使機械設(shè)備在生產(chǎn)中,不會發(fā)生不良,及時無人看守,機械本身也能產(chǎn)生附加值的“自動機械”。①.一切加工動作,全由機械進行,保持“人與機械分開”的狀態(tài)。②.無人監(jiān)視的情況下,一旦發(fā)生不良,機器馬上停止。……精益生產(chǎn)方式推進順序6自動化Editedby第三部分——精益生產(chǎn)推進順序32精益生產(chǎn)方式推進順序7指從上一個加工完成以后到下一個加工良品產(chǎn)出之前的時間。包括替換模具、車削物、變更基準作業(yè)。以及裝配物、零件等變換作業(yè)。①.需徹底實施5S基礎(chǔ)。②.準備時間:內(nèi)部準備時間+外部準備時間?!儞Q準備時間Editedby第三部分——精益生產(chǎn)推進順序33指為滿足顧客所要求的品質(zhì),籍人、物、設(shè)備及生產(chǎn)方式,保持品質(zhì)無懈可擊的綜合體系。①.即使只生產(chǎn)一件不良品,也應(yīng)該當(dāng)場究明原因并予解決。②.消除庫存、搬運、停滯的浪費,有效地制造產(chǎn)品。……精益生產(chǎn)方式推進順序8品質(zhì)保證③.將目前的生產(chǎn)方式“表格化”,定為標(biāo)準作業(yè)。④.一個個的制造,形成無不良的自動化生產(chǎn)線。⑤.不將不良品送到后工序。Editedby第三部分——精益生產(chǎn)推進順序34是作業(yè)指示及零件調(diào)配的依據(jù)。①.后工序至前工序拿取已被前工序用畢的看板。②.前工序只要生產(chǎn)后工序取去的數(shù)量?!嫔a(chǎn)方式推進順序9看板管理③.看板與現(xiàn)品一起流動,徹底執(zhí)行目視管理。④.為避免生產(chǎn)誤失,消除浪費,生產(chǎn)實施平準化。⑤.盡量減少看板的數(shù)量。Editedby第三部分——精益生產(chǎn)推進順序35是指讓大家一看就明白何者正常、何者有異常、何處有浪費的管理。①.以紅牌作戰(zhàn)與看板作戰(zhàn)進行目視的整理、整頓。②.利用指示燈傳達工程異常、零件供應(yīng)、刀具交換等訊息。……精益生產(chǎn)方式推進順序10目視管理③.制作生產(chǎn)管理看板,使大家知道生產(chǎn)線的作業(yè)狀況或停止內(nèi)容。④.標(biāo)志現(xiàn)場不良品區(qū)。Editedby第三部分——精益生產(chǎn)推進順序36保全指保養(yǎng)機械或設(shè)備,使之不發(fā)生故障,提高機械可利用率。安全指設(shè)計防止事故或者災(zāi)害發(fā)生的工廠構(gòu)造與規(guī)則,并遵守之。①.保全的習(xí)慣:清掃、給油、點檢。②.安全的要求:人機間保持距離、徹底執(zhí)行保全措施、嚴守規(guī)則、尋找真正原因并防止再發(fā)。……精益生產(chǎn)方式推進順序11保全·安全Editedby第三部分——精益生產(chǎn)推進順序37三種經(jīng)營思想成本中心思想售價=成本+利潤根據(jù)成本和計劃利潤決定售價僅適用于賣方市場售價中心思想利潤=售價-成本利潤根據(jù)售價變動屬于被動利潤型利潤中心思想成本=售價-利潤根據(jù)售價變化主動降低成本第四部分——排除浪費,降低成本38如何降低成本成本的構(gòu)成成本一般有以下要素組成:材料、人工、制造費用、消耗品、管理費用、設(shè)備、工資……等?如何降低成本消滅浪費!第四部分——排除浪費,降低成本39企業(yè)常見的浪費等待浪費搬運浪費不良浪費動作浪費加工浪費庫存浪費制造過多(過早)浪費缺貨損失8大浪費如何發(fā)現(xiàn)企業(yè)中的浪費現(xiàn)象第四部分——排除浪費,降低成本40無論如何,企業(yè)要想生存,首先必須獲得利潤,如果沒有利潤,企業(yè)將失去生存的條件。在不同的歷史階段,企業(yè)獲得利潤的方法是不同的。售價=成本+利潤(計劃經(jīng)濟時)售價—成本=利潤(市場經(jīng)濟時)售價—利潤=成本(精益思想TPS)利用成本倒留法可確保經(jīng)營的最終效果。第四部分——排除浪費,降低成本411.等待的浪費因斷料、作業(yè)不平衡、計劃不當(dāng)、以外等導(dǎo)致作業(yè)者處于等待狀態(tài)。工廠八大浪費之一①.生產(chǎn)線機種切換。②.工位間由于不平衡造成等待的浪費。③.機器設(shè)備故障導(dǎo)致等待的浪費。④.因為缺料等導(dǎo)致人和設(shè)備等待的浪費。⑤.生產(chǎn)計劃安排不平衡導(dǎo)致人機閑置?!谒牟糠帧懦速M,降低成本42等浪費待等待不創(chuàng)造價值
常見的等待現(xiàn)象:☆物料供應(yīng)或前工序能力不足造成待料
☆監(jiān)視設(shè)備作業(yè)造成員工作業(yè)停頓
☆設(shè)備故障造成生產(chǎn)停滯
☆質(zhì)量問題造成停工
☆型號切換造成生產(chǎn)停頓造成等待的常見原因:
☆線能力不平衡
☆計劃不合理
☆設(shè)備維護不到位
☆物料供應(yīng)不及時第四部分——排除浪費,降低成本432.搬運的浪費物料的放置、堆積、移動、整理等浪費。①.物料移動所需空間的浪費。②.人力、工具的占用。③.時間的浪費?!S八大浪費之二④.推車的移動。第四部分——排除浪費,降低成本44搬浪移動費時費力
搬運過程中的放置、堆積、移動、整理等都造成浪費。搬運是一種不產(chǎn)生附加價值的動作。搬運的損失,分為放置、堆積、移動、整列等動作浪費。1)物品移動所要的空間浪費2)時間的耗費3)人力、工具的占用4)搬運的物損費運空間、時間、人力和工具浪費第四部分——排除浪費,降低成本453.不良、修理的浪費工廠內(nèi)產(chǎn)生不良品,需要進行處置的時間、人力、物力上的浪費,以及由此產(chǎn)生的相關(guān)浪費。①.材料損失。②.設(shè)備、人員工時損失。③.額外處理人員的增加。④.影響生產(chǎn)。⑤.出貨延遲。⑥.產(chǎn)品降價。工廠八大浪費之三第四部分——排除浪費,降低成本46浪費不良不良造成額外成本
常見的等待現(xiàn)象:☆材料損失
☆設(shè)備折舊
☆人工損失
☆能源損失
☆價格損失
☆訂單損失☆信譽損失第四部分——排除浪費,降低成本47工廠八大浪費之四4.動作的浪費現(xiàn)場作業(yè)動作不合理造成的浪費。①.物品取放、反轉(zhuǎn)、對準等不合理。②.作業(yè)時轉(zhuǎn)身、大幅度動作。③.抬臂過高、過低等?!谒牟糠帧懦速M,降低成本48浪費多余動作增加強度降低效率
常見的12種浪費動作:①兩手空閑②單手空閑③作業(yè)動作停止④動作幅度過大⑤左右手交換⑥步行多動作⑦轉(zhuǎn)身角度大⑧移動中變換動作⑨未掌握作業(yè)技巧⑩伸背動作⑾彎腰動作⑿重復(fù)/不必要動作第四部分——排除浪費,降低成本49工廠八大浪費之五5.過分精確的加工浪費過分精確的加工或者多于的加工,造成不必要的人工浪費。①.多余的作業(yè)時間和輔助設(shè)備。②.生產(chǎn)資源如電、水等浪費。③.額外處理人員的增加。④.加工、管理工時增加。⑤.時間浪費、影響產(chǎn)量完成?!谒牟糠帧懦速M,降低成本50過剩的加工造成浪費
常見的加工浪費:☆加工余量
☆過高的精度
☆不必要的加工過剩加工造成的浪費:
☆設(shè)備折舊
☆人工損失☆輔助材料損失☆能源消耗浪費加工第四部分——排除浪費,降低成本51以下全是庫存浪費零部件、材料的庫存半成品的庫存成品的庫存已向供應(yīng)商訂購的在途零部件已發(fā)貨的在途成品庫存高度不良品調(diào)整時間長故障能力不平衡品質(zhì)不一致缺勤計劃有誤第四部分——排除浪費,降低成本52庫存的成因及其對策庫存的害處
☆造成額外成本
☆帶來缺貨風(fēng)險☆掩蓋問題和矛盾庫存的11大成因
☆賣方時代意識
☆積習(xí)難改☆產(chǎn)能不均☆集結(jié)性工序(工藝)☆“消化”不暢☆“侯鳥”作業(yè)☆討厭換?!钤碌宗s貨☆基準沒改☆顧及安全☆季節(jié)變動(淡旺季)第四部分——排除浪費,降低成本53逐步消除庫存逐步根絕浪費利潤最大化JustIn
Time適品·適量·適時流線化生產(chǎn)安定化生產(chǎn)平穩(wěn)化生產(chǎn)適時化生產(chǎn)第四部分——排除浪費,降低成本54☆對提高顧客滿意度有幫助嗎?有損害嗎?☆對提高企業(yè)效益有幫助嗎?有損害嗎?關(guān)于“”的兩個問題重要第四部分——排除浪費,降低成本556.庫存的浪費庫存量過大,資金積壓越多。工廠八大浪費之六①.產(chǎn)生不必要的搬運、堆積、尋找等動作。②.使先入先出作業(yè)困難。③.資金占用。④.場地占用。⑤.管理費增加。⑥.能力不足被掩蓋?!谒牟糠帧懦速M,降低成本56假設(shè)購入100萬資材,年利息10%,管理成本5%第0年100萬第4年40萬第1年85萬第5年25萬第2年70萬第6年10萬第3年55萬若報廢則為負值建立一個觀念:庫存是一種負債庫存的負債觀念576.制造過多的浪費庫存量過大,資金積壓越多。工廠八大浪費之六①.在制品積壓。②.使先入先出作業(yè)困難。③.增加周轉(zhuǎn)箱等設(shè)備成本。④.庫存增加。⑤.資金積壓。⑥.能力不足被掩蓋?!谒牟糠帧懦速M,降低成本58浪費違背JIT原則制造過多/過早制造過多/過早造成浪費:
☆造成在庫
☆計劃外/提早消耗
☆有變成滯留在庫的風(fēng)險☆降低應(yīng)對變化的能力工廠八大浪費之七第四部分——排除浪費,降低成本59損失缺貨造成機會損失
由于各種浪費消耗了企業(yè)資源,降低了經(jīng)營效率,反過來制約企業(yè)的訂單履行,造成缺貨損失:
☆緊急訂單造成額外成本
☆延遲訂單造成額外成本
☆訂單取消造成利潤損失☆客戶流失造成市場機會損失貨缺工廠八大浪費之八第四部分——排除浪費,降低成本60管理的實質(zhì)0-1+1增加價值提高產(chǎn)品和服務(wù)的附加價值消除浪費最大限度地減少不增值勞動創(chuàng)造性的管理活動封閉性的管理活動第四部分——排除浪費,降低成本611.兩手空閑具體操作中,出現(xiàn)兩只手均無事可做的時間段的浪費。工廠十二個動作的浪費-①2.單手空閑具體操作中,出現(xiàn)兩只手均無事可做的時間段的浪費。3.作業(yè)動作停止具體操作中,因操作順序不合理等原因?qū)е聞幼鞒霈F(xiàn)停頓的浪費。第四部分——排除浪費,降低成本624.動作太大動作幅度超出“經(jīng)濟動作”的范圍。5.左右手交換因零件、工具等位置不合適,導(dǎo)致拿取、使用過程中必須進行方向等變換的動作的浪費。6.步行多空手或移動距離過長等無價值的步行的浪費。工廠十二個動作的浪費-②第四部分——排除浪費,降低成本637.轉(zhuǎn)身角度大超出“經(jīng)濟動作”范圍而導(dǎo)致的浪費。8.移動中變換“狀態(tài)”因零件、工具等位置不合適,導(dǎo)致拿取、使用過程中必須進行方向等變換的動作的浪費。9.不明技巧不了解作業(yè)技巧而導(dǎo)致的時間浪費。工廠十二個動作的浪費-③第四部分——排除浪費,降低成本6410.伸臂動作超出“經(jīng)濟動作”范圍而導(dǎo)致的浪費。11.彎腰動作超出“經(jīng)濟動作”范圍而導(dǎo)致的浪費。12.重復(fù)/不必要動作因操作順序設(shè)置不合理,導(dǎo)致重復(fù)的或者不必要的各種動作浪費。工廠十二個動作的浪費-④第四部分——排除浪費,降低成本65經(jīng)濟動作經(jīng)濟動作范圍下限位置上限位置下限位置上限位置適合作業(yè)區(qū)域最適合作業(yè)區(qū)域第四部分——排除浪費,降低成本66整理(SEIRI):要與不要的東西分開,工作現(xiàn)場不要放置不需要的東西工廠里有很多的東西,如果空間不夠就很麻煩????要找空間,辦法是整理67
設(shè)備綜合效率=時間稼動率*性能稼動率*制品率85%以上每臺設(shè)備故障時間稼動率
(1)故障時間10分鐘以上者負荷時間-停止時間max1次/月負荷時間
前置每次調(diào)整前置90%以上
(2)作業(yè)作業(yè)時間調(diào)整max10min
空轉(zhuǎn)空轉(zhuǎn)、短暫停機性能稼動率
(3)短暫10分鐘以下者停機max3次/月理論CT╳產(chǎn)量
稼動時間
(4)速度CT實現(xiàn)周轉(zhuǎn)數(shù)提高15%以上95%以上
設(shè)備六大損失負荷時間停止損失稼動時間本體稼動時間速度損失設(shè)備SS第四部分——排除浪費,降低成本68(
溫馨提示
- 1. 本站所有資源如無特殊說明,都需要本地電腦安裝OFFICE2007和PDF閱讀器。圖紙軟件為CAD,CAXA,PROE,UG,SolidWorks等.壓縮文件請下載最新的WinRAR軟件解壓。
- 2. 本站的文檔不包含任何第三方提供的附件圖紙等,如果需要附件,請聯(lián)系上傳者。文件的所有權(quán)益歸上傳用戶所有。
- 3. 本站RAR壓縮包中若帶圖紙,網(wǎng)頁內(nèi)容里面會有圖紙預(yù)覽,若沒有圖紙預(yù)覽就沒有圖紙。
- 4. 未經(jīng)權(quán)益所有人同意不得將文件中的內(nèi)容挪作商業(yè)或盈利用途。
- 5. 人人文庫網(wǎng)僅提供信息存儲空間,僅對用戶上傳內(nèi)容的表現(xiàn)方式做保護處理,對用戶上傳分享的文檔內(nèi)容本身不做任何修改或編輯,并不能對任何下載內(nèi)容負責(zé)。
- 6. 下載文件中如有侵權(quán)或不適當(dāng)內(nèi)容,請與我們聯(lián)系,我們立即糾正。
- 7. 本站不保證下載資源的準確性、安全性和完整性, 同時也不承擔(dān)用戶因使用這些下載資源對自己和他人造成任何形式的傷害或損失。
最新文檔
- 2024年生態(tài)循環(huán)養(yǎng)雞場環(huán)保設(shè)施建設(shè)合同3篇
- 2024年環(huán)境污染治理技術(shù)合作合同
- 數(shù)學(xué)班主任期末工作總結(jié)推動學(xué)生數(shù)學(xué)學(xué)科素養(yǎng)的提高
- 2024棋牌室租賃合同范本
- 2024年試用期間工作合同6篇
- 2024年汽車行業(yè)經(jīng)銷商聯(lián)盟銷售合同范本3篇
- 2024年試用期限三天版標(biāo)準勞動協(xié)議示例版B版
- 2024年貨車運輸服務(wù)協(xié)議標(biāo)準版
- 2024建筑工程材料購銷合同范文
- 《鋼板樁施工工法》課件
- 玉溪大紅山鐵礦二期北采區(qū)采礦施工組織設(shè)計
- 中醫(yī)診療技術(shù)操作規(guī)程
- 2024年《多媒體技術(shù)與應(yīng)用》 考試題庫及答案
- 2024年外研版九年級英語上冊知識點總結(jié)
- 2024新教科版四年級上冊科學(xué)知識點總結(jié)精簡版
- 《朝花夕拾》閱讀推進課 教學(xué)設(shè)計-2023-2024學(xué)年統(tǒng)編版語文七年級下冊
- 項目駐場服務(wù)合同協(xié)議書
- 11SG102-3 鋼吊車梁系統(tǒng)設(shè)計圖平面表示方法和構(gòu)造詳圖
- DL∕T 1901-2018 水電站大壩運行安全應(yīng)急預(yù)案編制導(dǎo)則
- 三年級上冊100道口算練習(xí)題(各類齊全)
- 電動叉車充電區(qū)安全規(guī)程
評論
0/150
提交評論